Written by Shad Sechrist
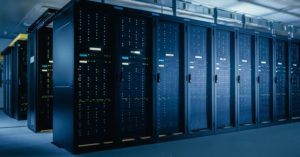
If you’re looking for ways to reduce data center operating costs, then lowering monthly energy bills is a great place to start. By far, the biggest contributor to high data center operating costs are these recurring expenses.
What drives your utility bill so high each month? In most data centers, it comes down to the operation of non-IT systems:
- Cooling and air handling
- Lighting
- Security cameras
To determine how much of your total power usage goes to systems that don’t provide compute services, you can calculate your data center’s power usage effectiveness (PUE). This ratio compares the total amount of power used by your data center to the amount of power delivered to its computing equipment. It also reveals how much energy is used for non-IT activities and systems.
PUE = total facility power / IT equipment energy
A high PUE indicates that your data center uses more power than it should to run equipment. A low ratio suggests that energy is used effectively to get compute work done.
As we examined the Uptime Institute’s 11th Annual Global Data Center Survey, we discovered that energy-efficiency progress has slowed down for many data centers.
From 2003 to 2010, for example, the data center industry made great strides in improving PUE. The average data center dropped from 2.5 to 1.6. In the last five years, however, the industry hit a plateau. The average PUE has been stagnant, sitting near 1.56.
When this PUE is translated to a percentage (by using the data center infrastructure efficiency [DCiE] metric), it shows that approximately 60% of energy entering the data center is used to power the non-IT systems we mentioned earlier—not the compute gear.
Newly constructed data centers designed to maximize energy efficiency typically see PUEs of 1.1 or 1.05—proof that this level of performance can be achieved. And while there’s plenty of new space on the horizon, most data centers have been running for years and rely on older systems.
Why is PUE Progress Slowing Down?
By now, most data center managers have had time to pick the low-hanging fruit, such as:
- Isolating supply and retain air through containment walls or using end-of-row doors on aisles to prevent air mixing.
- Using blanking panels to fill unused “U” positions in racks or enclosures and separate hot and cool air.
- Sealing holes in walls and raised floors with plenum-rated products.
- Replacing missing or poorly fitting floor tiles.
- Getting rid of underused or non-operational servers.
If your data center hasn’t implemented these best practices, now’s the time to do so. You’ll see an immediate improvement in energy use and lower data center operating costs.
The next phase of efficiency improvements, which can take PUE from 1.5 to 1.2 or 1.1, requires more time and money. Once you pick all your low-hanging fruit, here are some examples of what’s waiting higher up the tree.
Deploy Power Distribution Units (PDUs)
PDUs are like well-constructed power strips designed to be used in data centers. Today’s smart PDUs help data center managers remotely monitor power use, energy efficiency and environmental conditions.
They can track metrics like real-time power usage, data and event logs, the amount of current drawn by each PDU and the amount of current drawn by each outlet so you can optimize usage down to the device level.
This level of granularity is key. When you know exactly how much energy certain systems use, it becomes obvious as to where changes need to be made—even down to the rack level.
Install More Efficient Cooling Equipment
If you want to replace your legacy cooling equipment with new, more efficient systems to better control heat, there are many options to choose from. The right one for your data center depends on its size, location, configuration and unique design challenges.
You can choose to cool at the room level, the row level or the rack level (or use a combination), and there’s a long list of systems to choose from: computer room air conditioners (CRACs), liquid cooling and precision cooling are just a few examples.
If your cooling equipment is outdated, then it’s likely inefficient. Upgrading your system can reduce energy use and lower data center operating costs.
Invest in White Cabinets
Lighter-colored cabinets can conserve electricity in a few ways. Light colors like silver or white naturally reflect more light than dark colors (like black) because they have different light reflectance values (LRVs). For this reason, additional lighting is often needed to see labels and ports among dark cabinets.
When you lower lighting levels, you also reduce the amount of heat given off by the lighting system, which reduces cooling requirements. We estimate that swapping black enclosures for a lighter color leads to energy savings of between 1% and 2%.
Update Lighting
Modernize your lighting systems to take advantage of LED technology. LEDs are a good fit for data centers for many reasons:
- They generate less heat than fluorescents, which translates to lower cooling costs
- They use less energy than alternatives
- They offer lighting uniformity so all areas are equally bright, reducing shadows that make maintenance work difficult
Occupancy sensors and lighting zones are also effective ways to control data center operating costs. When no one’s in the data center, the lights will automatically shut off. (Depending on your surveillance equipment, you may need enough illumination for proper video capture, but many of today’s cameras can see in low-light and dark conditions.) When the lights are on, initial entry areas and halls don’t need to be as bright as equipment areas, and they can be zoned accordingly.
Keep People Out of the Data Center
Data centers spaces are built to process data, not host people. Keeping the data center as “hands-off” or “lights-out” as possible is another step you can take to reduce data center operating costs.
IT equipment can operate at higher ambient temperatures than those typically comfortable for people. If you can automate certain processes and reduce the need for onsite staff, then the space doesn’t need to be as cool.
Lights-out data centers may not be common yet, but COVID-19 revealed what these unmanned spaces may look like. In many cases, the examples proved that data centers can operate with little human involvement.
Find the original article here